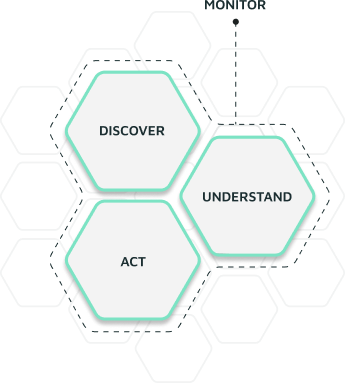
Integrate: Deploy process mining across ERP logistics, fleet management, and GPS tracking to analyze routes, truck use, and load consolidation. IoT sensors and real-time tracking enhance visibility into bottlenecks.
Discover: Identify underutilized trucks, inefficient routing, and empty trips that increase costs and emissions. Process mining pinpoints gaps in consolidation, loading delays, and fleet imbalances.
Understand: Logistics inefficiencies stem from poor load planning, scheduling, or last-minute transport changes. Partial loads raise fuel costs, emissions, and trips. Addressing these issues optimizes resource use.
Act: Use AI-driven route optimization, automated load consolidation, and dynamic fleet scheduling to cut empty trips and maximize capacity. Real-time adjustments boost efficiency and reduce costs.
Monitor: Track fleet utilization, fuel efficiency, costs, and CO₂ emissions via dashboards. Automated alerts flag routing inefficiencies, shipment delays, and missed consolidation for continuous improvement.
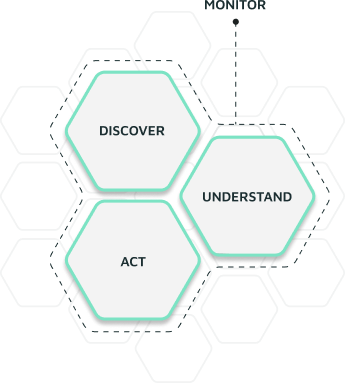
Integrate: Applied process mining to procurement workflows, linking demand forecasting with real-time inventory tracking. Supplier integration allowed automatic stock replenishment, while sales data from restaurant POS systems informed purchasing decisions.
Discover: Identified overstocking, inefficient purchasing patterns, and food wastage in buffet and restaurant services. Analysis revealed discrepancies between predicted and actual consumption, leading to excessive spoilage.
Understand: Analyzed sales data, supplier lead times, and consumption trends to optimize ordering. Seasonal fluctuations and event-driven demand were incorporated into forecasting models to fine-tune procurement cycles.
Act: Implemented automated restocking alerts and supplier integration to ensure timely replenishment of essentials. Dynamic pricing adjustments were introduced for perishable items nearing expiration to reduce waste.
Monitor: Used dashboards to track food usage, stock levels, and order fulfillment rates, adjusting procurement strategies dynamically. Automated alerts were set up to flag potential shortages before they impacted service operations.
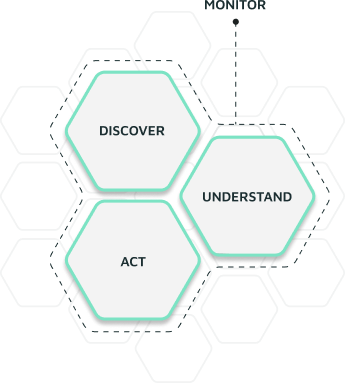
Integrate: Applied process mining to inventory and warehouse management systems, integrating historical sales data, market trends, and supplier lead times for enhanced forecasting accuracy.
Discover: Identified inconsistencies in inventory levels, frequent stockouts, and surplus stock buildup due to inaccurate demand planning. Analysis showed inefficiencies in reorder points and safety stock levels.
Understand: Assessed seasonal demand fluctuations, slow-moving inventory, and procurement cycles. Found that traditional forecasting models failed to account for sudden demand spikes or supplier constraints.
Act: Deployed AI-driven demand forecasting models, automated replenishment alerts, and dynamic stock level adjustments across multiple warehouse locations. Introduced just-in-time inventory strategies to reduce excess stock while ensuring availability.
Monitor: Used real-time dashboards to track stock movement, order fulfillment rates, and demand patterns, allowing continuous procurement and supply chain strategy adjustments.
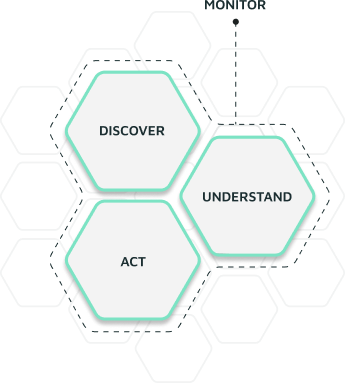
Integrate: Connected procurement, inventory, and logistics systems with process mining to analyze supplier performance and order fulfillment patterns. Integrated IoT-based shipment tracking for real-time visibility.
Discover: Identified delays in purchase order approvals, inconsistent supplier delivery schedules, and inefficiencies in distribution hubs. Data revealed bottlenecks in customs clearance and transportation routes.
Understand: Assessed historical supplier performance, seasonal demand fluctuations, and process inefficiencies. Found that redundant approvals and manual supplier interactions contributed to shipment delays.
Act: Implemented automated supplier performance scorecards, predictive ordering models, and dynamic route optimization for logistics partners. Introduced automated purchase order approvals for pre-vetted suppliers.
Monitor: Used real-time dashboards to track delivery lead times, order fulfillment rates, and supplier reliability. AI-driven alerts flagged potential disruptions, enabling proactive interventions.
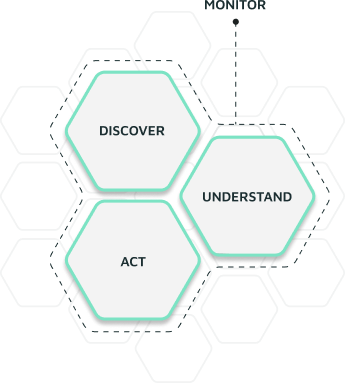
Connect the order processing system with the out-of-the-box connector for supply chain management systems. Configure relevant KPIs, including back order rate and order fulfillment time.
Process Mining identifies causes of back orders, such as supply chain disruptions and inventory shortages. Further analysis shows specific products and suppliers with frequent issues.
Improve inventory management, enhance supplier collaboration, and implement real-time tracking of orders and shipments.
Monitor the metrics back order rate and order fulfillment time to ensure continuous improvement in order processing efficiency.
Ready to unlock your business potential?
Enter your email below and we'll get back to you.