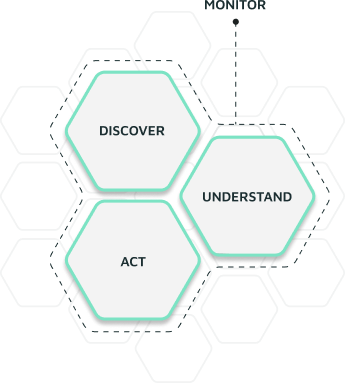
Integrate: Deploy process mining across ERP sustainability modules, IoT sensors, and ESG platforms to automate data collection for emissions, water, waste, and compliance. This removes data silos and ensures a reliable ESG reporting source.
Discover: Identify inefficiencies like missing emissions data, inconsistent waste tracking, and reporting delays. Process mining pinpoints manual bottlenecks, redundant workflows, and compliance risks.
Understand: ESG inefficiencies often stem from manual errors, fragmented data, or outdated monitoring. Delays may result from slow approvals, missing disclosures, or inconsistent reporting. Addressing these issues improves compliance, reduces errors, and streamlines reporting.
Act: Automate emissions tracking, waste monitoring, and ESG compliance validation using AI-driven anomaly detection and process automation, reducing errors and improving data accuracy.
Monitor: Use real-time ESG dashboards to track key metrics, trigger compliance alerts, and enable proactive sustainability improvements.
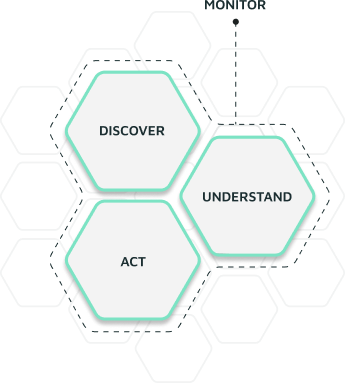
Integrate: Deploy process mining across ERP logistics, fleet management, and GPS tracking to analyze routes, truck use, and load consolidation. IoT sensors and real-time tracking enhance visibility into bottlenecks.
Discover: Identify underutilized trucks, inefficient routing, and empty trips that increase costs and emissions. Process mining pinpoints gaps in consolidation, loading delays, and fleet imbalances.
Understand: Logistics inefficiencies stem from poor load planning, scheduling, or last-minute transport changes. Partial loads raise fuel costs, emissions, and trips. Addressing these issues optimizes resource use.
Act: Use AI-driven route optimization, automated load consolidation, and dynamic fleet scheduling to cut empty trips and maximize capacity. Real-time adjustments boost efficiency and reduce costs.
Monitor: Track fleet utilization, fuel efficiency, costs, and CO₂ emissions via dashboards. Automated alerts flag routing inefficiencies, shipment delays, and missed consolidation for continuous improvement.
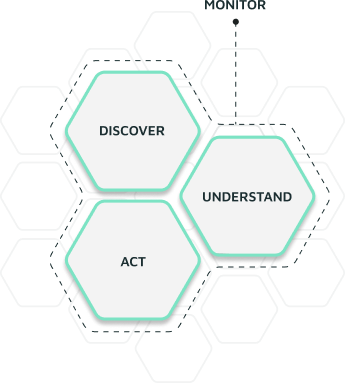
Integrate: Deploy process mining across ore tracking systems, milling operations, flotation circuits, and chemical analysis systems to capture real-time insights on material processing efficiency.
Discover: Identify inefficiencies in ore blending, grinding, chemical reagent usage, and recovery processes that lead to yield losses or excessive material wastage.
Understand: Analyze sources of recovery losses, suboptimal reagent dosing, and process variability, linking them to incorrect feed ratios, equipment inefficiencies, or poor real-time adjustments.
Act: Implement AI-driven real-time process control adjustments, optimize grinding and flotation parameters, and reduce reagent overuse to improve recovery efficiency.
Monitor: Set up real-time dashboards tracking ore recovery rates, chemical consumption, and plant throughput efficiency for continuous process improvement.
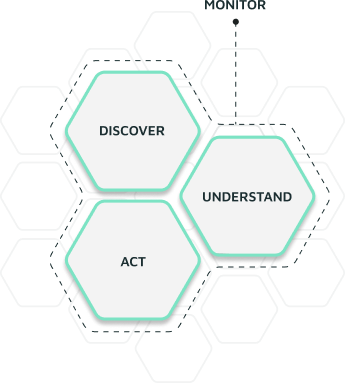
Integrate: Connect process mining with IoT sensors, CMMS, and ERP asset management to track real-time equipment health, maintenance logs, and failure patterns.
Discover: Identify failure points, underperforming assets, and inefficient maintenance by analyzing breakdowns, backlogs, and repeated part replacements.
Understand: Investigate root causes like overuse, poor lubrication, and excessive wear. Assess links to operational patterns, environmental conditions, or maintenance strategies.
Act: Use AI for predictive maintenance, automated work order prioritization, and optimized spare parts management, ensuring just-in-time servicing.
Monitor: Track MTBF, MTTR, and TCO via real-time dashboards for continuous maintenance optimization.
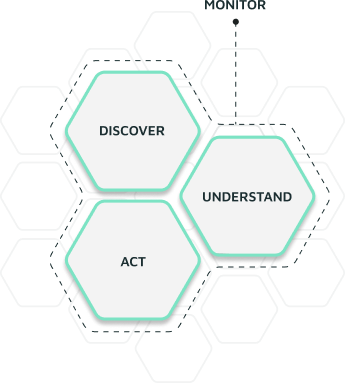
Integrate: Deploy process mining across ERP, fleet management, and IoT sensors to create a real-time digital twin, ensuring visibility into drilling, haulage, processing, and shipments.
Discover: Detect bottlenecks like truck idle time, delayed blasting, and plant congestion. Analyze load balancing to optimize material flow.
Understand: Identify root causes of slowdowns, downtime, and excess handling, such as poor shift planning, inefficient routes, and stockpile mismanagement.
Act: Use AI for haulage optimization, automated dispatching, and predictive scheduling to improve efficiency and reduce waste.
Monitor: Track KPIs like extraction efficiency, cycle times, stockpile levels, and energy use via real-time dashboards for continuous optimization.
Ready to unlock your business potential?
Enter your email below and we'll get back to you.