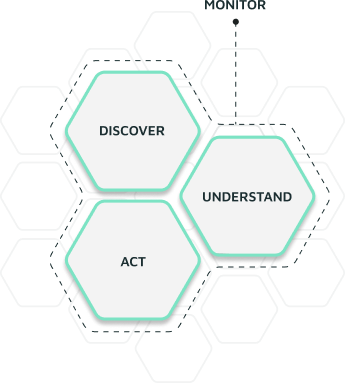
Integrate: Connected supplier management and ESG tracking platforms with process mining to assess sustainability compliance, carbon footprint impact, and regulatory adherence.
Discover: Identified non-compliant suppliers, high carbon-emitting procurement practices, and inefficiencies in sustainable sourcing strategies. Data revealed supply chain segments with excessive transportation emissions and unnecessary waste.
Understand: Assessed supplier sustainability ratings, green certification adherence, and regulatory requirements. Found that a lack of standardized sustainability metrics led to inconsistent compliance monitoring.
Act: Implemented automated supplier sustainability scoring, introduced preferred supplier programs for eco-certified vendors, and optimized procurement routes to lower emissions and transportation inefficiencies.
Monitor: Used dashboards to track supplier compliance, sustainability progress, and emissions data, ensuring continuous improvement in green procurement. AI-driven insights flagged areas for further carbon footprint reductions.
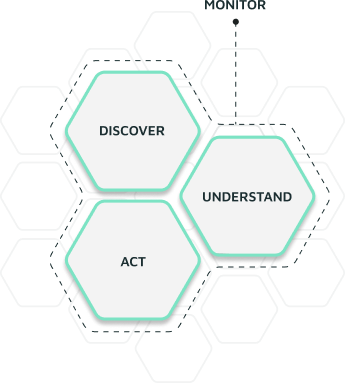
Integrate: Connected procurement, inventory, and logistics systems with process mining to analyze supplier performance and order fulfillment patterns. Integrated IoT-based shipment tracking for real-time visibility.
Discover: Identified delays in purchase order approvals, inconsistent supplier delivery schedules, and inefficiencies in distribution hubs. Data revealed bottlenecks in customs clearance and transportation routes.
Understand: Assessed historical supplier performance, seasonal demand fluctuations, and process inefficiencies. Found that redundant approvals and manual supplier interactions contributed to shipment delays.
Act: Implemented automated supplier performance scorecards, predictive ordering models, and dynamic route optimization for logistics partners. Introduced automated purchase order approvals for pre-vetted suppliers.
Monitor: Used real-time dashboards to track delivery lead times, order fulfillment rates, and supplier reliability. AI-driven alerts flagged potential disruptions, enabling proactive interventions.
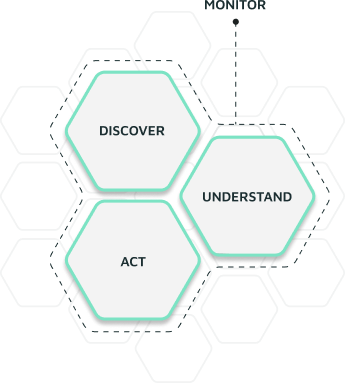
Analyze water usage data across all production processes using process mining tools. Identify critical points where water is used excessively or wasted.
Identify processes with high water consumption and pinpoint inefficiencies and leaks. Study historical patterns to understand usage fluctuations and peak times.
Implement water-saving technologies, optimize production schedules, and repair leaks to reduce water usage. Introduce water recycling and reuse systems to minimize fresh water consumption.
Continuously monitor water consumption metrics to ensure sustained water efficiency. Use sensors and IoT devices to track real-time water usage and detect anomalies.
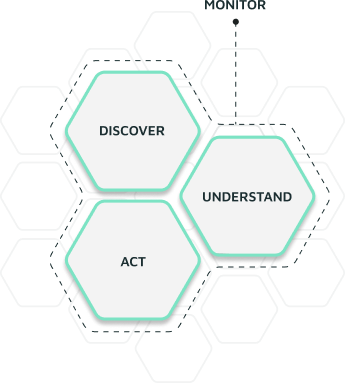
Analyze energy consumption patterns across various operations using process mining. Identify the key processes and equipment that are the largest consumers of energy.
Identify high-energy-consuming processes and pinpoint inefficiencies contributing to excessive energy use. Analyze historical data to find trends and irregularities in energy consumption.
Implement energy-saving technologies and optimize operational schedules to reduce peak energy usage. Introduce energy-efficient practices and equipment to minimize waste.
Continuously track energy consumption metrics to ensure sustained energy efficiency improvements. Regularly review energy reports to identify new opportunities for savings.
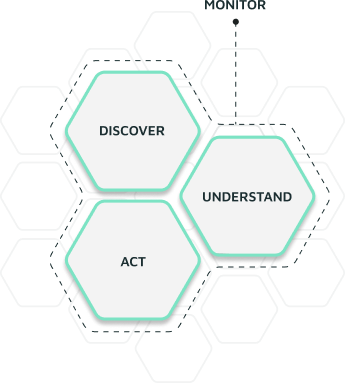
Map out the supply chain processes to identify high-emission areas and inefficient logistics. Use process mining to visualize the entire supply chain and highlight bottlenecks.
Analyze supplier practices and transportation routes to identify opportunities for sustainability improvements. Evaluate the environmental impact of each stage in the supply chain.
Optimize logistics to reduce transportation emissions, engage with suppliers to improve their ESG practices, and implement green logistics solutions. Develop partnerships with eco-friendly suppliers and logistics providers.
Track carbon emissions and supplier compliance metrics to ensure continuous improvement in supply chain sustainability. Implement a continuous monitoring system to track the progress and effectiveness of sustainability initiatives.
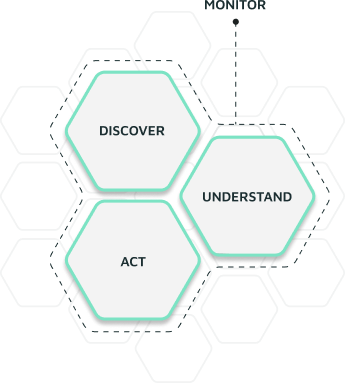
Connect the make-to-order production system with the out-of-the-box connector for manufacturing execution systems (MES). Configure relevant KPIs, including production lead time and on-time delivery rate.
Process Mining reveals bottlenecks in production and delays in material procurement. Further analysis identifies specific products and processes causing delays.
Streamline production scheduling, improve supplier coordination, and implement predictive maintenance to reduce downtime.
Monitor the metrics production lead time and on-time delivery rate to ensure continuous optimization of the production process.
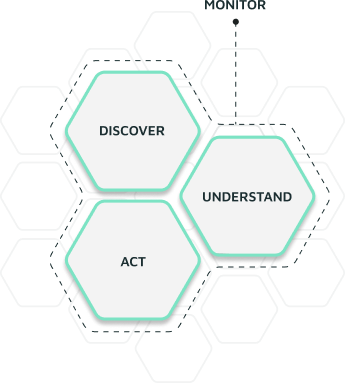
Connect the internal audit process with the out-of-the-box connector for audit management systems. Configure relevant KPIs, including audit coverage rate and findings per audit.
Process Mining identifies areas with high risk and frequent non-compliance. Further analysis shows specific processes and departments where these issues occur.
Prioritize audit activities based on risk levels and automate routine compliance checks to free up auditors for high-value tasks.
Monitor the metrics audit coverage rate and findings per audit to ensure continuous improvement in audit effectiveness.
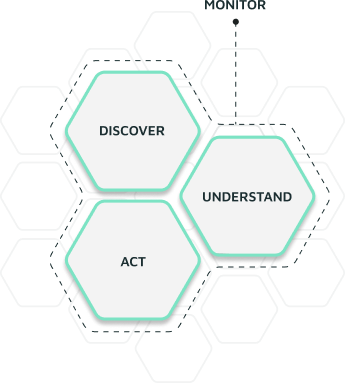
Connect the order processing system with the out-of-the-box connector for supply chain management systems. Configure relevant KPIs, including back order rate and order fulfillment time.
Process Mining identifies causes of back orders, such as supply chain disruptions and inventory shortages. Further analysis shows specific products and suppliers with frequent issues.
Improve inventory management, enhance supplier collaboration, and implement real-time tracking of orders and shipments.
Monitor the metrics back order rate and order fulfillment time to ensure continuous improvement in order processing efficiency.
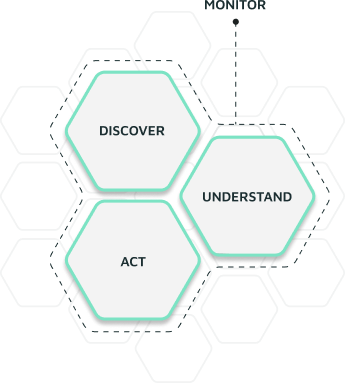
Connect the SAP accounts payable process with the out-of-the-box connector for SAP accounts payable. Configure relevant KPIs, including % of discounts captured and the impacted value.
Process Mining reveals a low % of discounts captured. Further analysis shows which suppliers are paid later than the due date, and the impacted value.
Automate invoice payment for suppliers with an early payment discount program, and trigger alerts to accounts payable team when payment exceeds the due date.
Monitor the metric % Discounts Captured to continuously maximize the value of cash discounts.
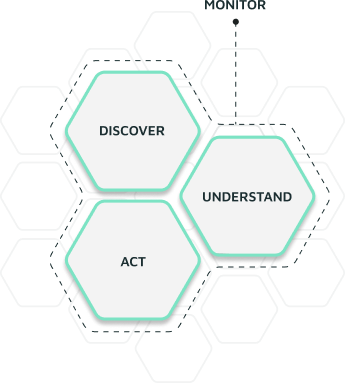
Connect the financial and supply chain management systems with the out-of-the-box connectors. Configure relevant KPIs, including Cash Conversion Cycle (CCC), Days Inventory Outstanding (DIO), Days Sales Outstanding (DSO), and Days Payable Outstanding (DPO).
Process Mining identifies bottlenecks in the supply chain, invoicing, and payment processes. Further analysis reveals specific suppliers, products, or customers that impact the CCC.
Streamline inventory management by implementing just-in-time (JIT) practices, improve invoice accuracy and speed up the billing process, and negotiate better payment terms with suppliers to extend DPO.
Monitor the metrics Cash Conversion Cycle (CCC), Days Inventory Outstanding (DIO), Days Sales Outstanding (DSO), and Days Payable Outstanding (DPO) to ensure continuous optimization of working capital.
Ready to unlock your business potential?
Enter your email below and we'll get back to you.